Today we often take for granted the quality of the silica in the HPLC column. This may be a reasonable assumption for the high-quality columns produced today, but it is not a guarantee, especially for columns that have been on the market for more than 10 years.
When HPLC was first developed in the late 1960s and early 1970s, the silica used as the support for the stationary phase in the column was that derived from natural sources. Naturally occurring silica, of course, is comes from the hard shells of ancient sea creatures. To obtain silica for column packing, the bulk silica was ground to a fine powder and then sized with some sort of sieving procedure. At first, this was just the use of soil-sieve screens to isolate a fraction of particles in the 37-44 µm range that could be dry-packed into columns. Later, as slurry packing techniques were developed, 10 µm particles could be packed. These were sized using a centrifugal flow of air or other technology.
Figure 1
Silica is an amorphous polymer of silicon (Si) and oxygen. At the surface, the polymer terminates in -Si-OH groups, referred to as silanols. The early materials, being of natural origin, were quite impure. One of the many contaminants were metal ions, in particular iron and aluminum (or aluminium, depending on your geography!), often at concentrations of >100 ppm. These ionic groups (Figure 1) form great ion-exchange sites for ionized acids, and as such resulted in packing materials that gave badly tailing peaks for acidic solutes. A more important problem was that if the metals were adjacent to silanol groups (which is going to be the normal case in a silica matrix), they withdrew electrons from the adjacent silanol, enhancing ionization of the silanols, especially at high pH. This is illustrated in the right-hand example of Figure 1. These activated silanol groups interacted strongly as cation-exchange sites for ionized bases. The resulting chromatograms showed strong retention and badly tailing peaks for basic solutes. These older, low-purity silicas are referred to as Type-A, or acidic silicas today.
The fix for the metal problem seems pretty obvious – remove the metals! The first attempts at this were to leach out the metals by treating the silica with acid to remove exposed metals. One of the pioneering products of this type were the “DB” phases (deactivated for bases) from Supelco. As technology improved, synthetic silica was developed, and the starting reagents could be chosen with reduced metal content. Reduction of metals and increased silica purity is a bit of a moving target, with the most recently introduced materials generally of higher purity than older materials. The lowest-metal silicas today have
The progression toward lower-metal silicas began in the late 1970s and continues today, with an ongoing effort to further reduce the metal content of Type-B silicas. However, if the column you are using is a new product introduced sometime after 1995-2000, it is likely that it is of the Type-B variety. If all else fails, check the column specifications or ask the supplier if it is made of high-purity, Type-B silica.
This blog article series is produced in collaboration with John Dolan, best known as one of the world’s foremost HPLC troubleshooting authorities. He is also known for his research with Lloyd Snyder, which resulted in more than 100 technical publications and three books. If you have any questions about this article send them to TechTips@sepscience.com
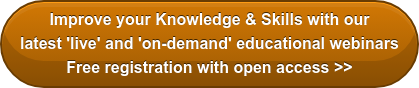